Do I have a boat or a pile of scrap wood in the shape of a boat?
That was what I was asking myself after I was finished gluing the panels together.
It started out OK. I got everything in order. I bought some extra syringes to practise with. I bought laquer thinner and denatured alcohol have on hand. I donned a respirator mask and nitrile gloves. I changed gloves whenever I noticed any epoxy on them at all. This way I didn't smear the glue all over my shop, my tools and the boat.
Step one: Practise. I screwed the pumps into the bottles of epoxy resin and hardener. I primed them and tossed out the first squirt that came out of each, since these weren't metered. Next I added two pumps of each into a disposable plastic bowl. I mixed well then added four spoonfuls of thickener (silica). I was shooting for the thickness of "thin mustard." What exactly is that? I played with it a bit and tried using it with a syringe on some scrap wood.
Step two: Add masking tape to the inside seams at the bow and stern to try to contain any drips.
Step three: Start gluing for real. This step should have been "Think", but I was nervous enough about this whole gluing thing that I was worried if I stopped to think, I wouldn't start again. So I mixed up another batch. Two pumps apiece. Five spoonfuls of silica. Mix well. Is it thick enough? Load it into a syringe. Close eyes. No, wait, better leave them open. Start injecting the thickened epoxy into the "lapstitch" joints. It was hard to apply it evenly so it had a consistant level, but it seemed to be working. I checked underneath - no drips. After mixing and using another batch, and gluing up four joints, I took a half-day break.
When I returned this morning, my previous work had set. I still don't know how long it will take to cure. I made two more batches and glued up the last four joints. I had half of a batch left. With this I went over yesterday's work and added glue to places I had obviously missed or where I hadn't added enough glue.
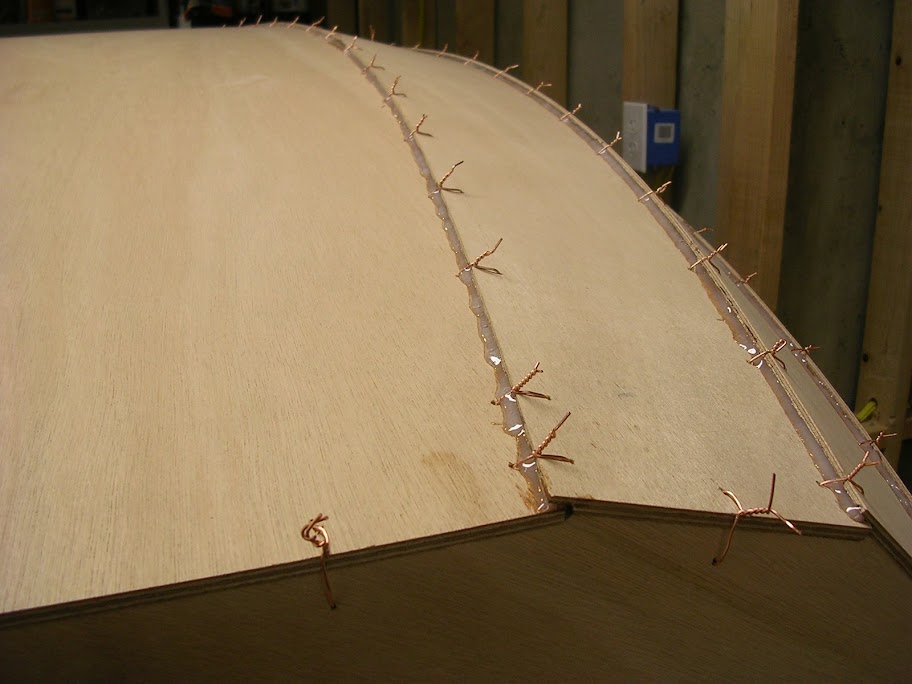
I saw three things that concerned me. First, the glue was adhering to the wires. It was supposed to flow underneath them without touching them, but at least half of my wires were attached to the glue in the joint beneath them. Second, the joints I had done yesterday were "lumpy". They evened out somewhat but were definitely uneven. Third, at the ends I could see that the epoxy hadn't completely filled the joint at the bottom. The area to be filled looks like a triangle in cross-section. They glue hadn't filled the very bottom of the triangle.
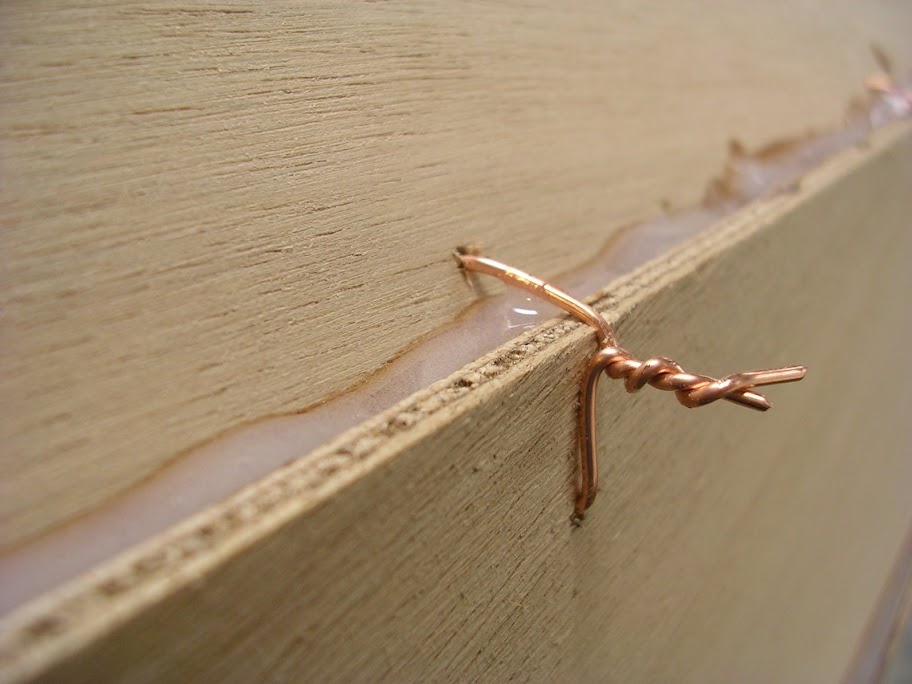
Looking back (I always do my best thinking in hindsight), I now realize that I added too much thickener to my epoxy. I guess I had "mayonaise" and not "thin mustard". Thinner epoxy would have filled in the joint more completely and "self-leveled" better.
What to do? I could only think of one thing to do. Panic.
So I began to panic, convinced that my boat was completely ruined. I was worried about the cosmetic damage of the lumpy seams, but I was even more concerned that the joints were too glue-starved and that I had done structural damage.
My wife calmed me down and suggested I call CLC for advice. So I gave them a call. They are really going to regret providing me with free technical support by the time this boat is done. I describe my woes to one person, who thinks the boat is still OK, but he has me talk with someone who I think was John. He assures me that it isn't ruined. I will have to sand out the high spots in the seams, but he says I would have had to fill in the low spots with epoxy thickened with wood flour anyway. As far as structural issues, he didn't think I had any, but if I wanted, I could try injecting unthinned epoxy from the inside once the boat was flipped back upright. Good thing I still have a syringe left over.
Bottom line: I think I still have a boat and not a pile of scrap wood and epoxy.